Valencia, 20 April 2020
The Coronavirus emergency has created an unprecedented global demand for protective masks. Not only for sanitary use as for the population at large. To satisfy the demand, the first stage has been to test the available tisssues and develop a model mask without valve. The second one was to stablish contact with companies to manufacture them.
The Conselleria of Sustainable Economy, Productive Sectors, Trade and Labor, with the collaboration of the Association of Textile Entrepreneurs of the Valencian Community (Ateval, a member organization of the Spanish Intertextile Council, CIE) and the Technological Textile Institute (Aitex), is leading a project that allows the manufacture of large-scale surgical masks in the companies of the Valencia Region. This project has brought togheter he knowledge of the textile sector of Ateval and Aitex’s experience in innovation and labs.
Two companies have provided the fabric for the production of surgical masks and five are manufacturing masks thanks to the adaptation of their machinery and production processes to the current situation. Creaciones Euromoda is one of these companies.
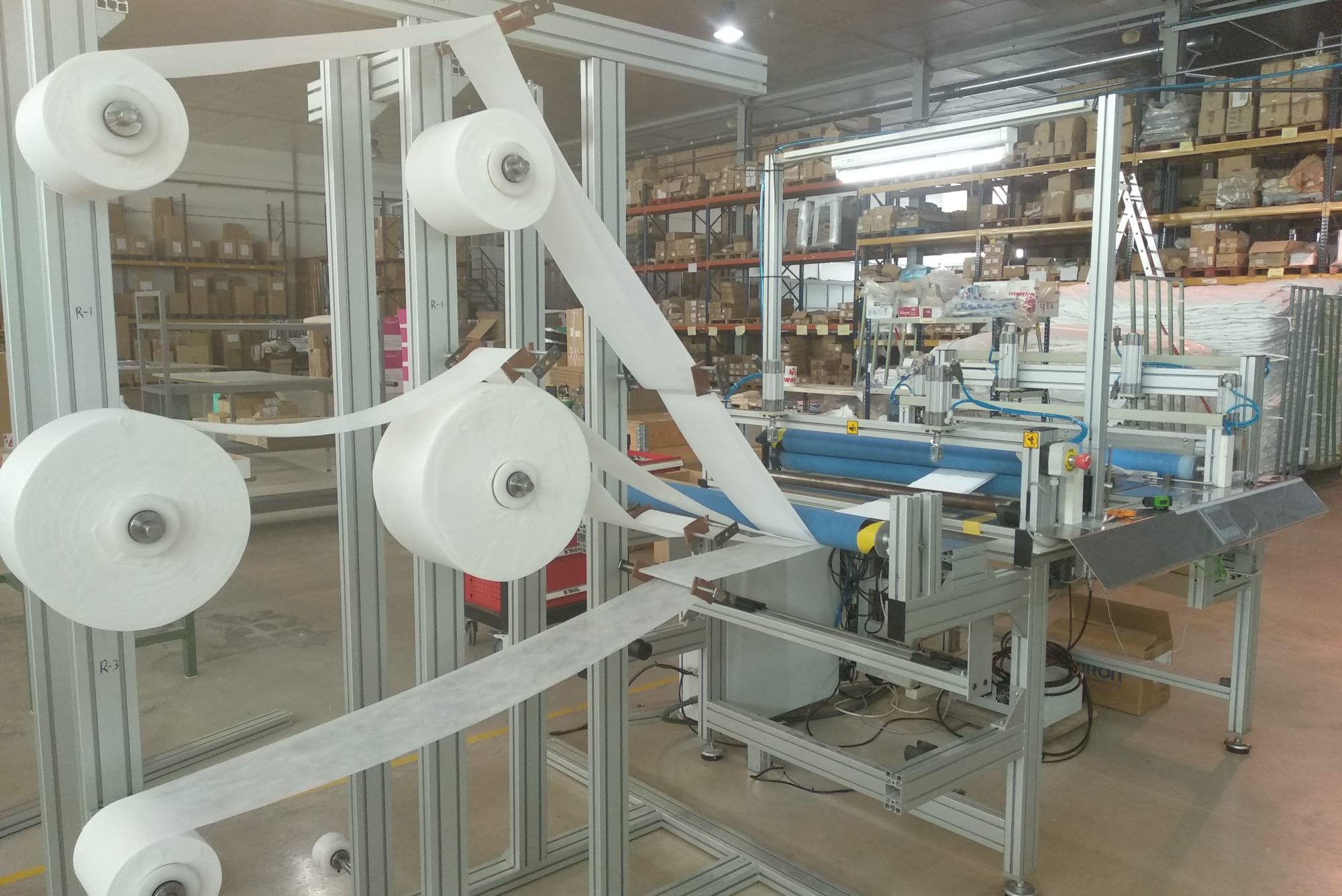
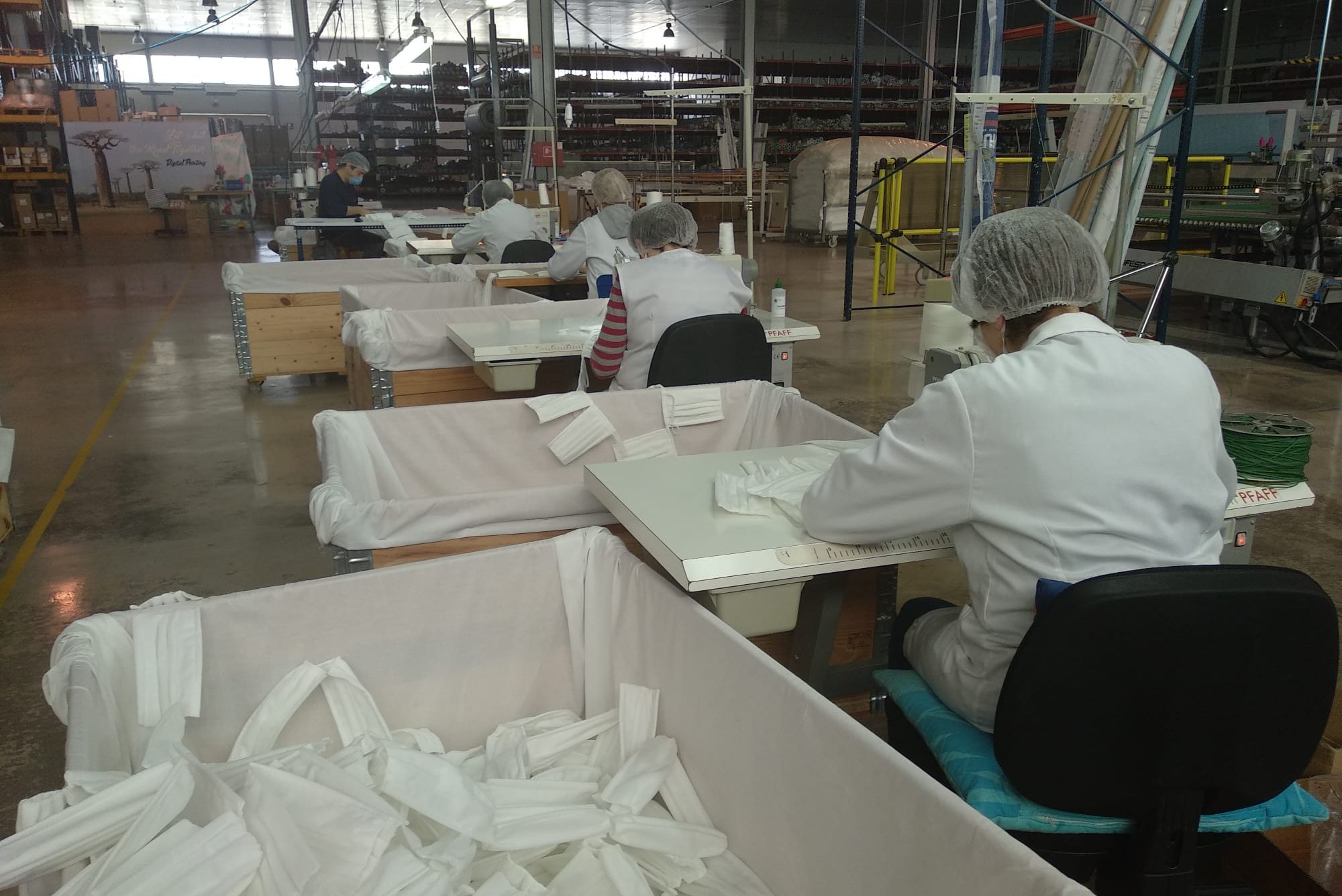
Creaciones Euromoda is a pioneering company in home textile innovation with more than 30 years of dedication and a portfolio of clients, firms and designers at national and international level.
Digital printing technology allows them to create quality prints on any type of fabric with millions of combinations of designs and colours. Their main production is bed linen and duvet covers.
At the beginning of the emergency, they manufactured hygienic masks to be distributed free of charge to the local population.
To start the homologated production they have acquired two flat sewing machines as they only had 6. The machines have been adapted according to the specifications of the mask procedure.
Adaptations have been made to apply the twisband. They have also had to modify the ultrasonic cutting and sealing machine, used in their production process of the cushion fillings, so that the “sandwich” of fabric (composed of five layers) is sealed and cut to the regulation size, automating most of the production process.
Now they are producing more than 6000 masks/day.
The company is already certified and produces an approved product following all health guidelines and Requirements.