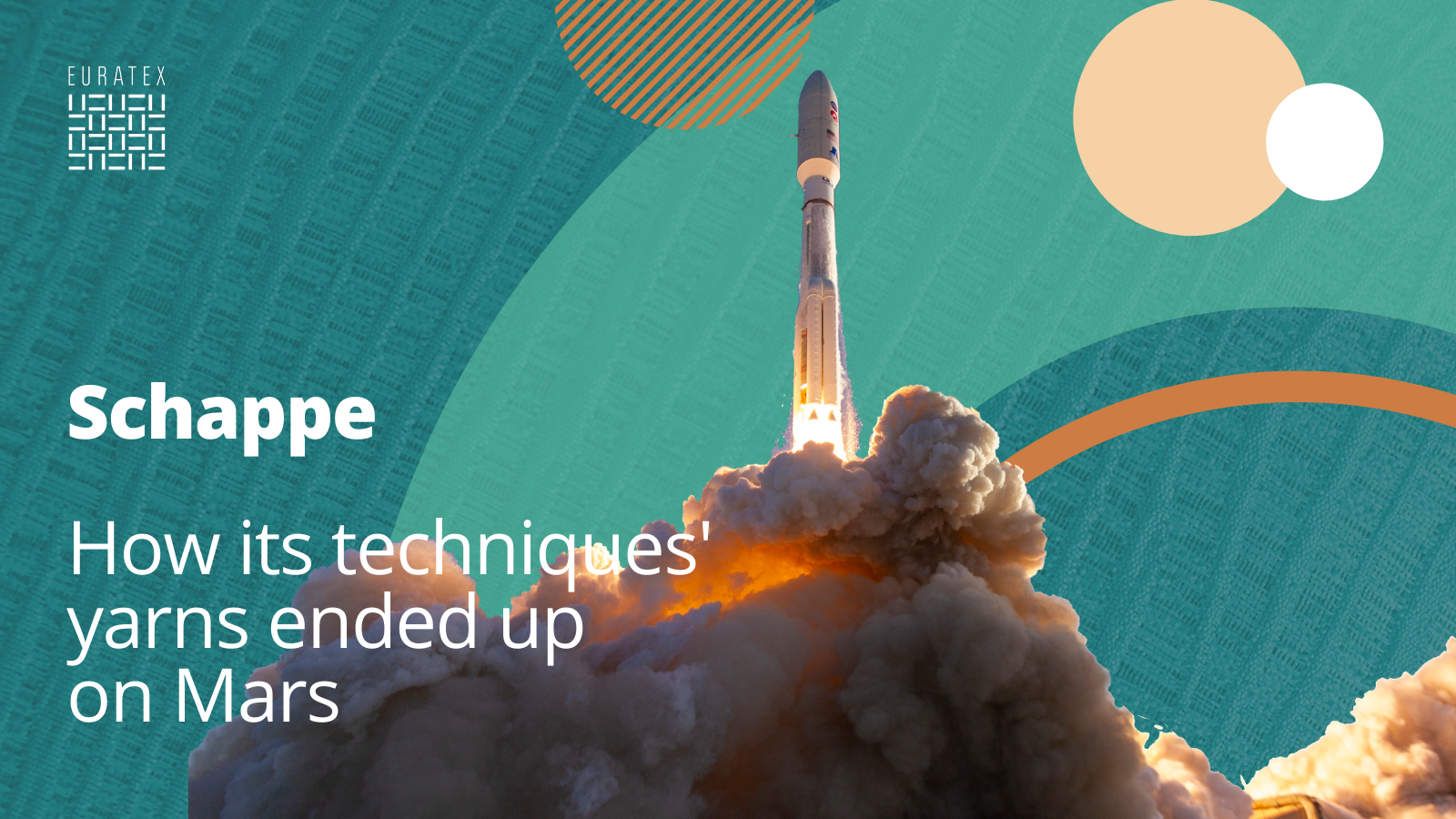
Last July, Nasa’s Mars 2020 mission and the Perseverance robot kept millions of viewers around the world in suspense. Among the French know-how on board, the technical yarns of the Schappe Techniques will serve as a heat shield for the capsule during its return to earth, in 10 years.
Specializing in the development of technical yarns in its spinning manufacture, Schappe Techniques employs 110 employees in the Vosges area, a historical textile region in France. Aramides, Dynema, kevlar, wires or carbon, the company converts more than 30 different materials into technical yarns, relying on Schappe’s unique stretch breaking technique whereby a long continuous filament is successively stretched and broken to remove weak points and transformed into fragmented but resistant and regular yarns. The company adapts 250 machines for each customer use and carries out precision work close to haute couture. The sprities and manual cleaning of thefiber guarantee its strength. These unique know-how and continuous innovation with its partners allow it to address cutting-edge applications. “There may be 4 or 5 companies in the world who know how to develop and manufacture this type of yarn,” comments Laurent Chaigneau, the company’s chief executive.
Schappe’s know-how is recognized around the world. The company works in France and Europe as well as in Japan and the USA, thanks to the strong partnerships it has built.
Some of Schappe’s yarns are involved in the manufacture of PPE (firefighter, police, or military protection suits) because of their thermal performance. “We are working in co-development with material manufacturers like Kermel to improve the fire-resistant properties of textiles, and at the other end of the chain with companies that weave or knit these protections. Today, with the new product developed, we can guarantee that firefighters’ uniforms made with these wires can withstand 2 consecutive fires,” explains Laurent Chaigneau.
As with the Mars 2020 capsule, some composite and carbon wires are used to build thermoformed products for space and the military (rockets, helmets). “The fabric can be up to 30 or 40 cm thick, then heated and consolidated to protect metal parts like the rocket booster that must have high heat resistance.” It is also found on the French Rafale jet fighters, or the wire of the Eurofighter’s parachutes.
In Japan, the silky and resistance of Schappe’s technical yarns have been appreciated for more than 50 years for the manufacture of kimonos, handcrafts or string art.
The company continues to expand its markets on niche applications such as the supply of metal wires for automotive tooling or carbon wires for pump seals in the nuclear or chemical industry.
The company also recruits operators that it trains in-house as well as technicians.